In the world of precision machinery, the Diodon HP30 stands out as a crucial component for industries ranging from engineering to military applications.
But how do you create something as specialized and powerful as the Diodon HP30? Whether you’re a seasoned engineer or someone interested in learning about this device, understanding the intricate process behind crafting the Diodon HP30 is an invaluable skill.
The Diodon HP30 is not your typical everyday device; it’s a high-performance tool that requires careful design, engineering, and assembly to function at its peak. The technology behind it involves the combination of sophisticated materials and mechanical processes that need to be executed to perfection.
This guide will walk you through the essentials of making the Diodon HP30, covering everything from its design and components to assembly and testing. Let’s dive into this fascinating process and learn what makes the Diodon HP30 so unique.
Contents
- 1 Understanding the Diodon HP30: What It Is and Why It Matters
- 2 Step 1: Designing the Diodon HP30: Blueprints and Initial Planning
- 3 Step 2: Manufacturing the Components of the Diodon HP30
- 4 Step 3: Assembling the Diodon HP30: Bringing All the Pieces Together
- 5 Step 4: Testing and Quality Control: Ensuring the Diodon HP30 Performs Flawlessly
- 6 Conclusion:
- 7 FAQ’s
- 7.0.1 What is the Diodon HP30 used for?
- 7.0.2 What materials are used in making the Diodon HP30?
- 7.0.3 How does the assembly process work for the Diodon HP30?
- 7.0.4 How do engineers test the Diodon HP30?
- 7.0.5 Is the Diodon HP30 customizable for specific applications?
- 7.0.6 What are the key features of the Diodon HP30?
Understanding the Diodon HP30: What It Is and Why It Matters
The Diodon HP30 is a high-performance, multi-purpose device that is essential in various industrial applications.
Known for its precision, durability, and efficiency, it is used in sectors like aerospace, engineering, and military operations. At its core, the Diodon HP30 is engineered to meet stringent requirements for accuracy, safety, and functionality, which is why it’s a sought-after tool in demanding environments.
This device operates using a complex set of mechanisms that are highly customized to meet specific operational needs. Understanding the purpose of the Diodon HP30 is vital before delving into the manufacturing process.
Whether used for mechanical work, precision measurement, or as a part of a larger system, the HP30’s design allows it to perform multiple functions with extreme reliability. By breaking down its components and their interactions, you can grasp why it’s such a valuable asset in the professional world.
Step 1: Designing the Diodon HP30: Blueprints and Initial Planning
The creation of the Diodon HP30 begins with its design phase, where engineers translate ideas into precise, technical blueprints. This initial step is critical because the functionality of the final product heavily depends on the design accuracy.
- Blueprint Creation: Using advanced CAD software, engineers design every component of the HP30. These blueprints consider the overall structure, the arrangement of mechanical parts, and the necessary tolerance levels. The design phase ensures that every part will fit together seamlessly.
- Material Selection: The materials used in crafting the Diodon HP30 are carefully chosen for their strength, weight, and durability. Depending on the application, metals, plastics, or even ceramic composites are used for different parts of the device. Each material’s properties must align with the intended use of the HP30.
- Prototype Development: Once the design is set, a prototype is created to test the functionality. Prototypes help identify potential issues early, whether it’s in terms of performance, durability, or ease of use. This step allows engineers to refine the design before moving on to the next stages of production.
Step 2: Manufacturing the Components of the Diodon HP30
Once the design is finalized, the next step is the manufacturing of individual components. This is a delicate process that involves precision machining and careful assembly of small but complex parts.
- CNC Machining: Using Computer Numerical Control (CNC) machines, parts such as gears, motors, and casing are crafted to the exact specifications from the design. These machines offer high precision and can create even the most complex components with minimal error.
- Component Testing: After each component is manufactured, it undergoes rigorous testing to ensure it meets the required standards. Testing can involve mechanical stress tests, electrical testing, and tolerance checks to make sure that each piece will function perfectly in the final assembly.
- Sub-Assembly: Some components are assembled in smaller sub-assemblies before the final product is put together. These sub-assemblies, such as the motor housing, sensor units, or control systems, are carefully checked for alignment, functionality, and interoperability.
Step 3: Assembling the Diodon HP30: Bringing All the Pieces Together
After the components are manufactured, they are ready to be assembled into the final product. This step requires skilled labor, advanced tools, and precise techniques to ensure everything fits together perfectly.
- Precision Assembly: Each component is carefully placed and attached to the main structure. This may involve using screws, fasteners, or welding techniques to secure parts in place. Assembly must be done with extreme attention to detail, as even the slightest misalignment can affect the device’s functionality.
- Integrating the Power System: One of the most critical parts of the assembly is the power system. The HP30 relies on a well-integrated system of batteries, motors, and electrical circuits. Engineers must ensure that the power system is both efficient and safe.
- Final Integration: Once all the main parts are assembled, the device is integrated with its control systems, sensors, and interfaces. This allows the device to function properly in its intended environment, whether for aerospace applications, engineering measurements, or military operations.
Step 4: Testing and Quality Control: Ensuring the Diodon HP30 Performs Flawlessly
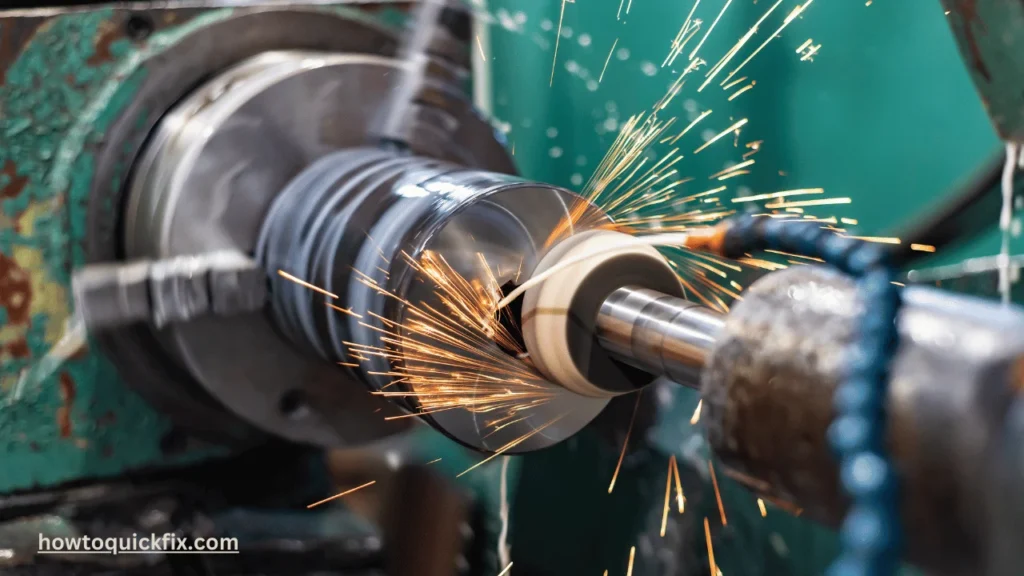
Before the Diodon HP30 can be put into use, it must undergo a thorough testing and quality control phase to ensure that it operates at full capacity and meets safety standards.
- Functional Testing: The device is tested in real-world conditions to ensure all of its features work correctly. This includes testing for operational efficiency, accuracy, and speed. Engineers monitor the HP30’s performance closely to make any necessary adjustments.
- Safety Testing: Given that the Diodon HP30 is used in sensitive industries, safety is paramount. The device undergoes stress testing, overload testing, and electrical safety checks to prevent any potential hazards during its use.
- Final Inspection: The last stage involves a final inspection of the device. Technicians check for cosmetic defects, verify that all components are properly installed, and ensure the product matches the original design specifications.
Conclusion:
Creating the Diodon HP30 is a complex, multi-step process that combines advanced design techniques, precision manufacturing, and rigorous testing. Each phase—from blueprints and material selection to assembly and quality control—is crucial in ensuring that the final product functions as intended.
By understanding the intricacies involved in crafting this high-performance tool, you can appreciate the level of expertise and attention to detail required to bring the Diodon HP30 to life.
Whether you’re a professional in the field, a student of engineering, or just an enthusiast, knowing how to make the Diodon HP30 can deepen your understanding of precision technology and open doors to new opportunities in the world of high-performance machinery.
The Diodon HP30 is a testament to the power of engineering innovation and the impact of sophisticated tools on modern industries.
FAQ’s
What is the Diodon HP30 used for?
The Diodon HP30 is a high-performance device used in engineering, aerospace, and military applications for precise measurements, mechanical work, and system integration.
What materials are used in making the Diodon HP30?
The Diodon HP30 utilizes a combination of metals, plastics, and ceramic composites depending on the specific part and its function.
How does the assembly process work for the Diodon HP30?
Components are carefully assembled using precision techniques, such as CNC machining, manual assembly, and welding.
How do engineers test the Diodon HP30?
The device undergoes functional testing, safety checks, and stress tests to ensure performance, accuracy, and reliability.
Is the Diodon HP30 customizable for specific applications?
Yes, depending on the industry, the Diodon HP30 can be customized with specific modules or features to meet particular requirements.
What are the key features of the Diodon HP30?
Key features include precision in mechanical operation, efficiency in performance, and reliability for demanding environments.